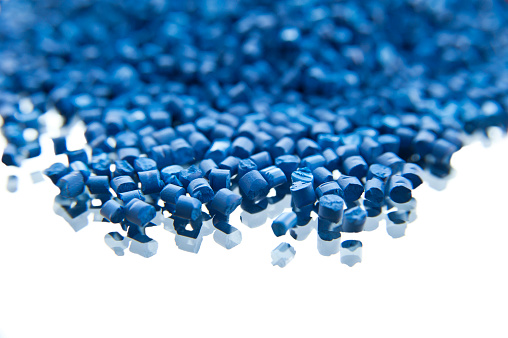
PLASTIC INJECTION MOLDING
Plastic injection molding in its simplest form is a process where we inject raw plastic material into a custom designed mold to produce our customer’s parts. We utilize our latest technologies and over 70 years of experience to build a better product for our customers.
Our Injection Molding Capabilities
• Horizontal Injection Molding up to 3300 TONS
• Structural Foam Molding + Structural Web
• 1oz to 600oz part capacity
• In-Mold Labeling and Decorating
• Twin & Two-Shot Injection Molding
• Two Color and Soft-Shot Over-Molding
• High Cavitation Molding
• Compression/Transfer Molding
• Vertical Injection Molding
• Gas Assist Molding
• Insert Molding
• Stack molds
LARGE PART MOLDING
Commercial Plastics is a leader in Large Part Molding with over 40 years experience and tonnage range up to 3300 tons. Our Illinois and Minnesota plants were specifically built for large part molding with a custom underground material handling systems with 16 silos able to hold 3 million pounds of raw material. We optimize material handling, part handling, quality, cosmetics, and logistics that large part molding demands. All of these components help produce the parts that keep your manufacturing projects running on time and to exacting standards.
In injection molding, particularly when dealing with large-part molding, choosing the right partner can be key to the success of your job. Commercial Plastics’ large-tonnage molding capabilities make us distinctively qualified to handle all your largest projects.
CPC Large Tonnage Molding Advantages
• Central locations for optimal shipping costs
• Quick change over systems for JIT
• Robotic Cells with 4 to 6 axis robots on all our large tonnage presses
• Porcelain material handling systems for abrasive materials
• Railroad direct access
• Returnable packaging logistics management
• Gas-Assist equipped on all our large tonnage presses
• Highly aesthetics parts with molded-in color
• Large mold build experience and management with worldwide partners
• High volume production
• Many secondary operations and assembly capabilities
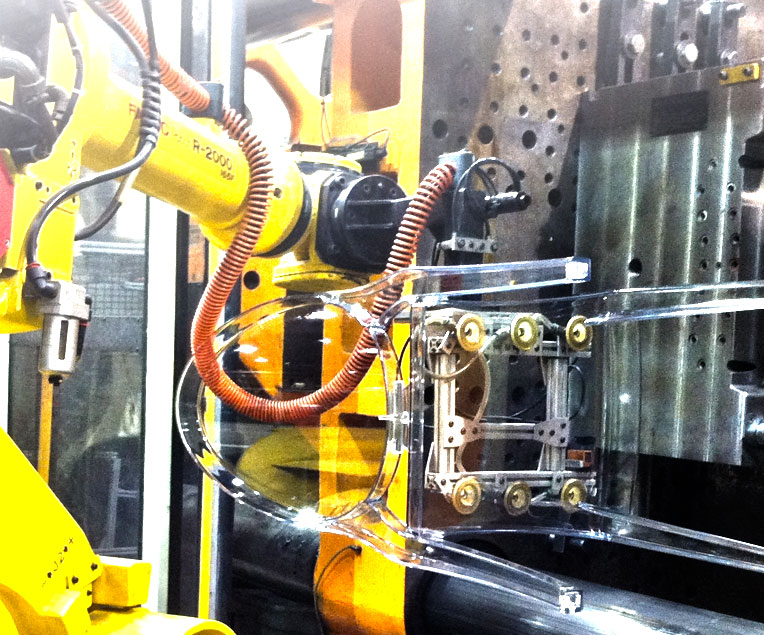
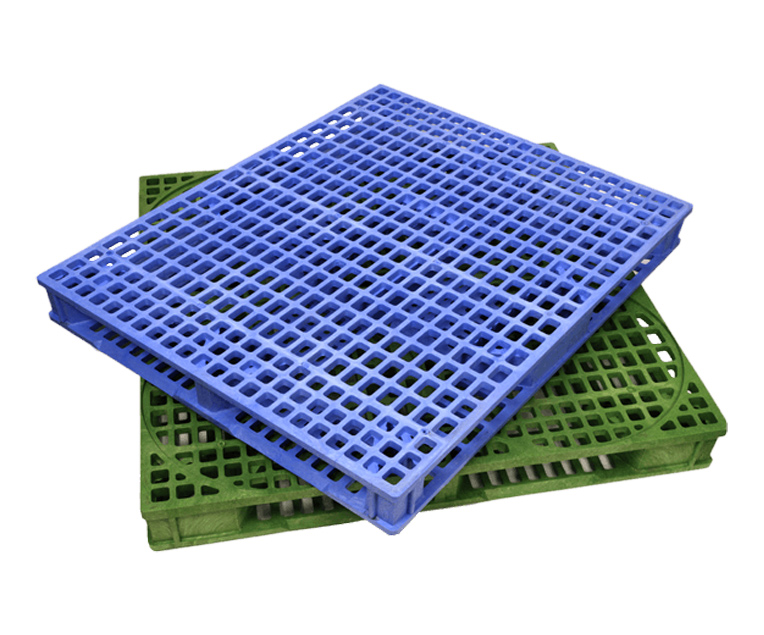
STRUCTURAL FOAM MOLDING
Structural Foam Molding can be broken down into several processes and techniques. Imperial Plastics is one of the pioneers in the industry using both Low Pressure Multi Nozzle Structural Foam / Web and High Pressure Injection Foam. Structural Foam molding can be processed using commodity resins as well as engineered grade resins. The process requires an inert gas (nitrogen) or a pelletized chemical blowing agent. The process is to mix the inert gas / blowing agent with the specific resin of choice inside the barrel or extruder.
The resin is then injected into the mold. Injection pressures are much lower than straight injection molding, as the mold front fills the cavity of the mold the gas expands and packs out the cavity. As the mold front fills the cavity it creates a hard surface against the walls of the mold. The center section of the nominal wall is where the cell structure / foam occurs. Typical wall sections for Structural Foam range from .180” to .250”. Thicker wall sections are common but will control cycle times. Typical weight reductions will range from 8 to 15 percent.
There are tooling advantages to the Low Pressure Structural Foam process. With the injection pressures being significantly lower than the standard injection process, tooling can be constructed out of aluminum instead of steel. Choosing the right tool material is dependent on the types of resin selected and the accumulated volumes expected for the tool life. A steel tool may be required if the resin of choice is a glass filled material or an aggressive abrasive material.
CPC Structural Foam Molding Advantages
- Central locations for optimal shipping costs
- Quick change over systems for JIT
- Robotic Cells with 4 to 6 axis robots on all our large tonnage presses
- Returnable packaging logistics management
- Gas-Assist equipped on all our large tonnage presses
- Thick Wall Section Molding
- Large mold build experience and management with worldwide partners
- High and Low volume production
- Many secondary operations and assembly capabilities
- Part weight reduction
STRUCTURAL WEB MOLDING
If your heavy wall sectioned part requires a more cosmetic surface Imperial Plastics offers Multi-Nozzle structural web molding. This process is similar to multi-nozzle structural foam molding except nitrogen is not introduced during the melting process. Instead, melted plastic is shot into the mold and gas is subsequently injected to pack out the part. This produces a part with a solid skin with hollow cross sections. This process typically requires additional tonnage (larger press) versus traditional multi-nozzle structural foam.
Our engineers can assist your design team to develop a component incorporating proper web channel geometry. Key benefits include; greatly improved surface finish on large parts often reducing the need for painting, part weight reduction, and sink elimination.
CPC Structural Web Molding Advantages
- Central locations for optimal shipping costs
- Heavy wall low pressure built for cosmetic surface
- Robotic Cells with 4 to 6 axis robots on all our large tonnage presses
- Returnable packaging logistics management
- Thick Wall Section Molding
- Large mold build experience and management with worldwide partners
- High and Low volume production
- Reduce the need for painting
- Part weight reduction and sink elimination
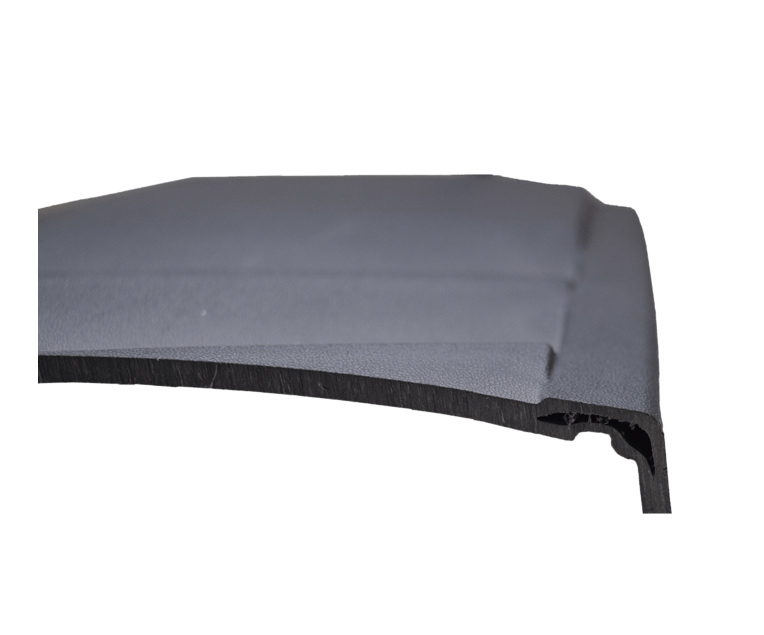
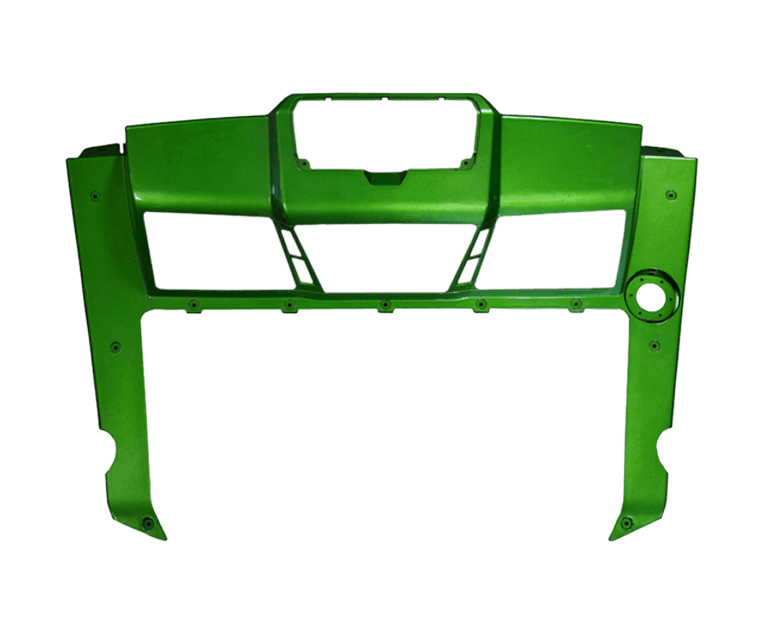
PAINTING / SHIELDING
We have the capability to paint with water based and urethane based paints. Parts are prepped using one of our four sanding booths providing a dust free environment for paint adhesion. Paints are applied in one of our four paint booths, typically over two base coats of primer. We specialize in applied texture finishes in single or two-tone paint schemes, and EMI / RFI shielding. All painted parts run through one of our two UV drying ovens or natural gas oven for proper curing at temperatures between 100F – 140F.
POST MOLDING DECORATING
Plastics are unique in that decoration and color can be added prior, during or after fabrication. The different post mold decorating methods provide different capabilities and benefits. They can be used for graphics application, aesthetics, multi-color and traceability to name a few. The decision of which post mold decorating option to use depends on your requirements and application.
Applications
• In-Mold Labeling & Decorating
• Painting/Shielding – In-house
• Multi-Color Hot Stamping
• Multi-Color Pad Printing
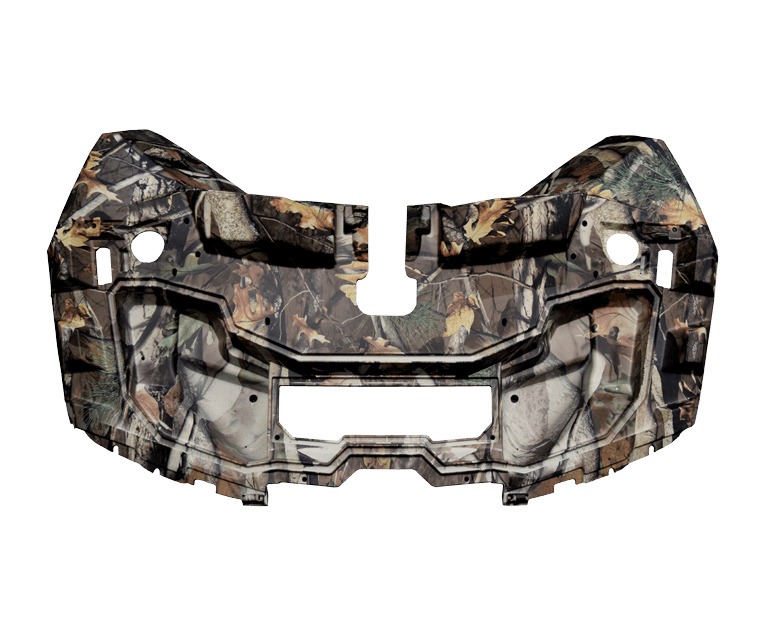
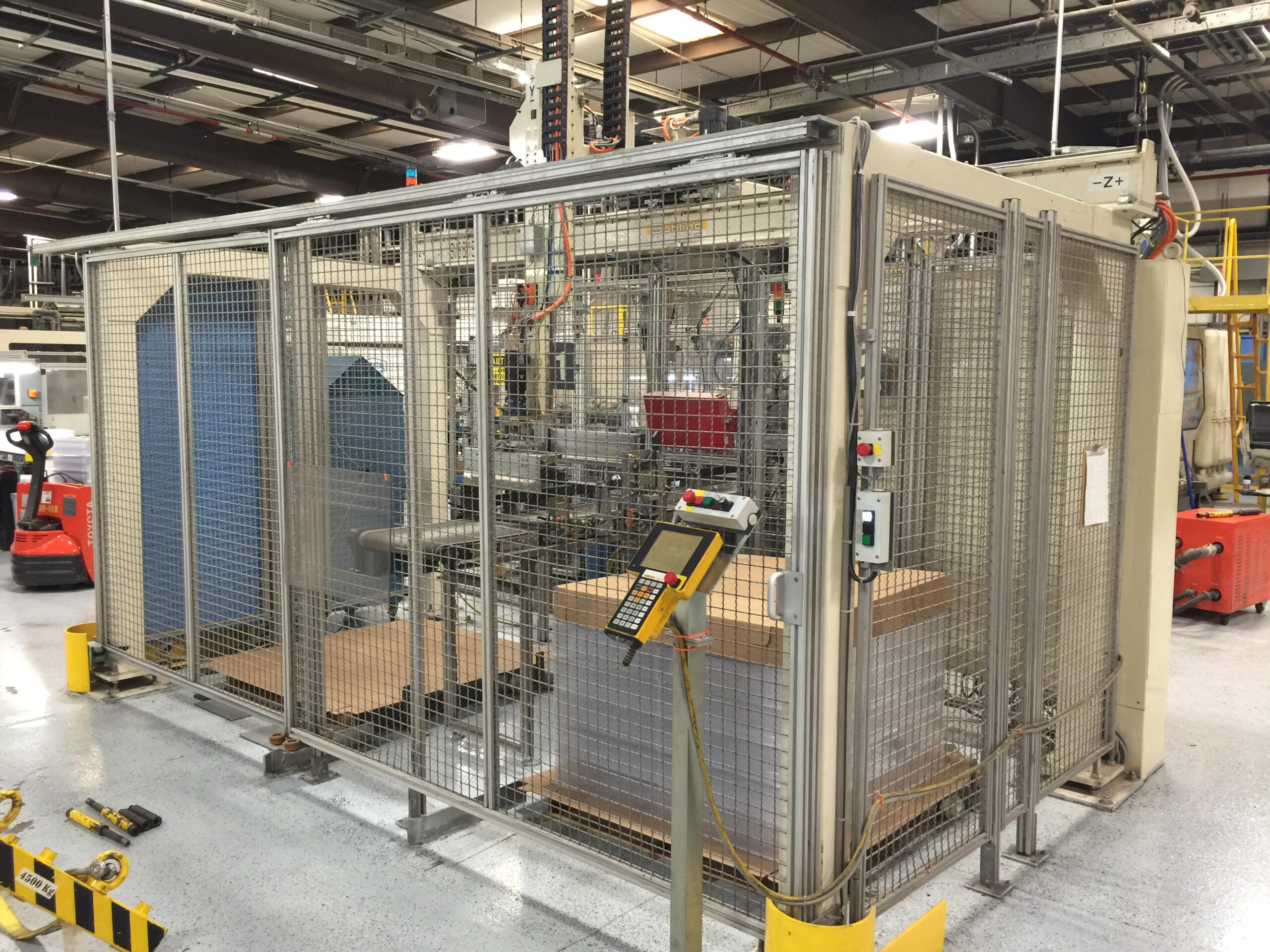
AUTOMATED ASSEMBLY AND PACKAGING
We specialize in automation assembly with millions of assemblies monthly. We have over 10 years of automated assembly and packaging experience from simple to intricate part assemblies to 100% automated palletizing. Our automation specialists can develop single cell to multi-cell automation systems to meet your demanding applications.
Advantages
• Reduce production and assembly cost
• Decrease in assembly cycle time
• Improved quality and reliability
• Reduce waste
COMPRESSION MOLDING
Compression molding is a method of molding in which we use thermoset materials as replacement to metal, and certain thermoplastic materials for demanding applications. This method is used for specific applications were certain physical properties of the material are needed. We have over 45 years of experience in this demanding industry with a range up to 550 tons.
Advantages
• Weight and noise reduction
• Part complexity and corrosion resistance
• Retention of physical properties at high ambient temperatures
• Ease of replacing metal by nearly matching the metal part geometry
• The ability to mold in inserts and rib stiffeners
• Dimensional control and stability
• High Heat resistance
• Electrical insulation
Applications
• Major appliance parts
• Demanding electrical components
• Oil and Gas components
• Industrial light housings
• HVAC components
• Electric motor and power transmission
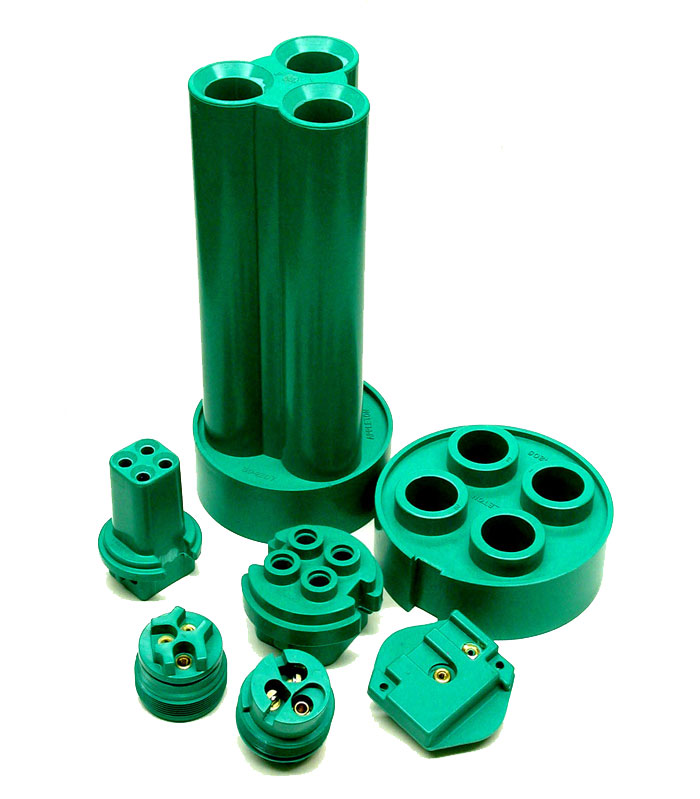
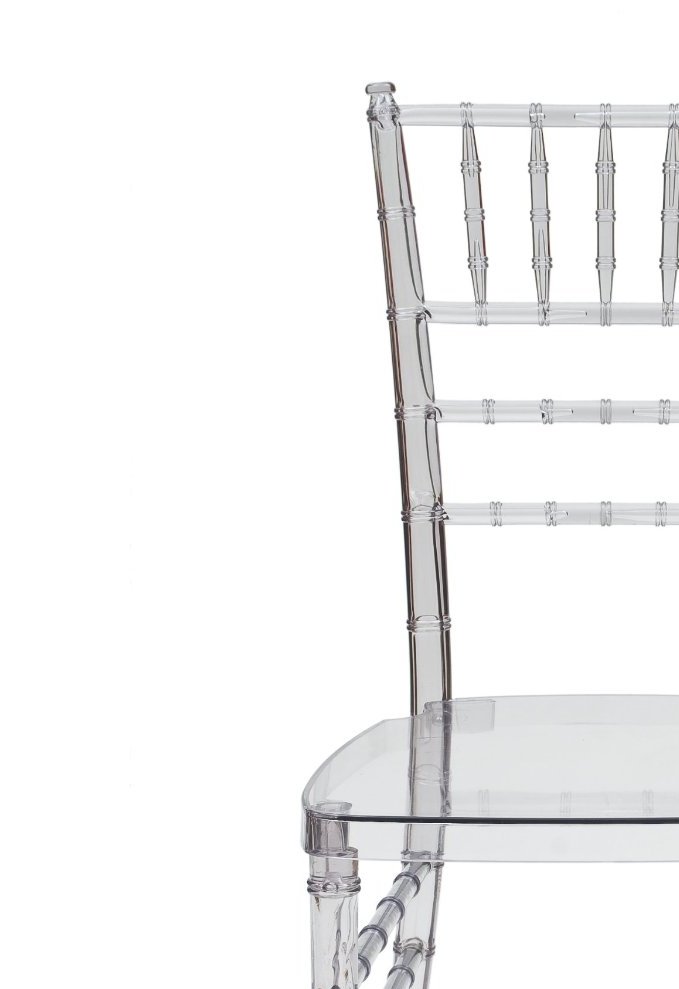
GAS-ASSIST MOLDING
Gas Assist Injection Molding is a low-pressure process utilizing nitrogen gas to apply uniform pressure throughout the molded plastic part. We produce our own nitrogen with an in-house compressor and booster.
Gas Assist Injection Molding allows CPC the freedom to design plastic parts without the restrictions and limitations inherent to conventional molding.
Thin wall parts with heavy ribs, bosses and gussets are formed to high standards of flatness without sink marks or long cycle times. Long shapes are produced without multiple drops or hot runner systems, eliminating knit lines and lowering tooling costs. Multiple parts with complex design and differing wall thickness are molded as a single part without defect. Clamp tonnage requirements are dramatically reduced by 50% or more in most gas assist applications.
WHY?
• Freedom of style and design
• Rigidity improvement
• Simplification of the tools
Reduction of clamping force
• Elimination of the sink marks
• Reduction in the cycle time
• Saving in polymer cost
• A better respect of the form (elimination of warpage)
HOW?
There are several methods of gas injection:
• The partial filling of cavity with polymer followed by gas.
• The complete filling of cavity and hollowing by gas
• By compacting the plastic material and by compensating the shrinkage during the packing step.
• By pushing the plastic material into a over-flow cavity.
• By driving back the plastic material towards the screw.
The parameters related to gas injection are, the time lag compared to the beginning of polymer injection, duration of gas applied, the level of pressure and its profile.
IN-MOLD LABELING AND DECORATING
Commercial Plastics has invested in the latest In-Mold Labeling and Decorating technology with pre-cut roll-fed technology. This new technology eliminates the need to cut the labels in-line. This allows for thinner labels with a more robust construction that replaces the cut and stack method and traditional roll fed method.
We have over 10 years of in-mold labeling and decorating experience used in many different applications. We have partnered with the top label makers keeping up with the latest technology as the IML industry innovates. Our systems are designed for sequential barcode reading and barcode lot traceability for medical and healthcare applications.
Advantages for In-mold labeling and decorating
In-mold labeling and decoration has many advantages over conventional decorating methods. These advantages include:
• Waste reduction – elimination of liner waste from PS or Heat Transfer decorations
• In-line barcode lot traceability
• In-line Device History Recording
• Scrap Reduction
• Better label and marking permanence
• Improved package or product design
• Improved recycling
• Reduced cost compared to other plastic decorating methods
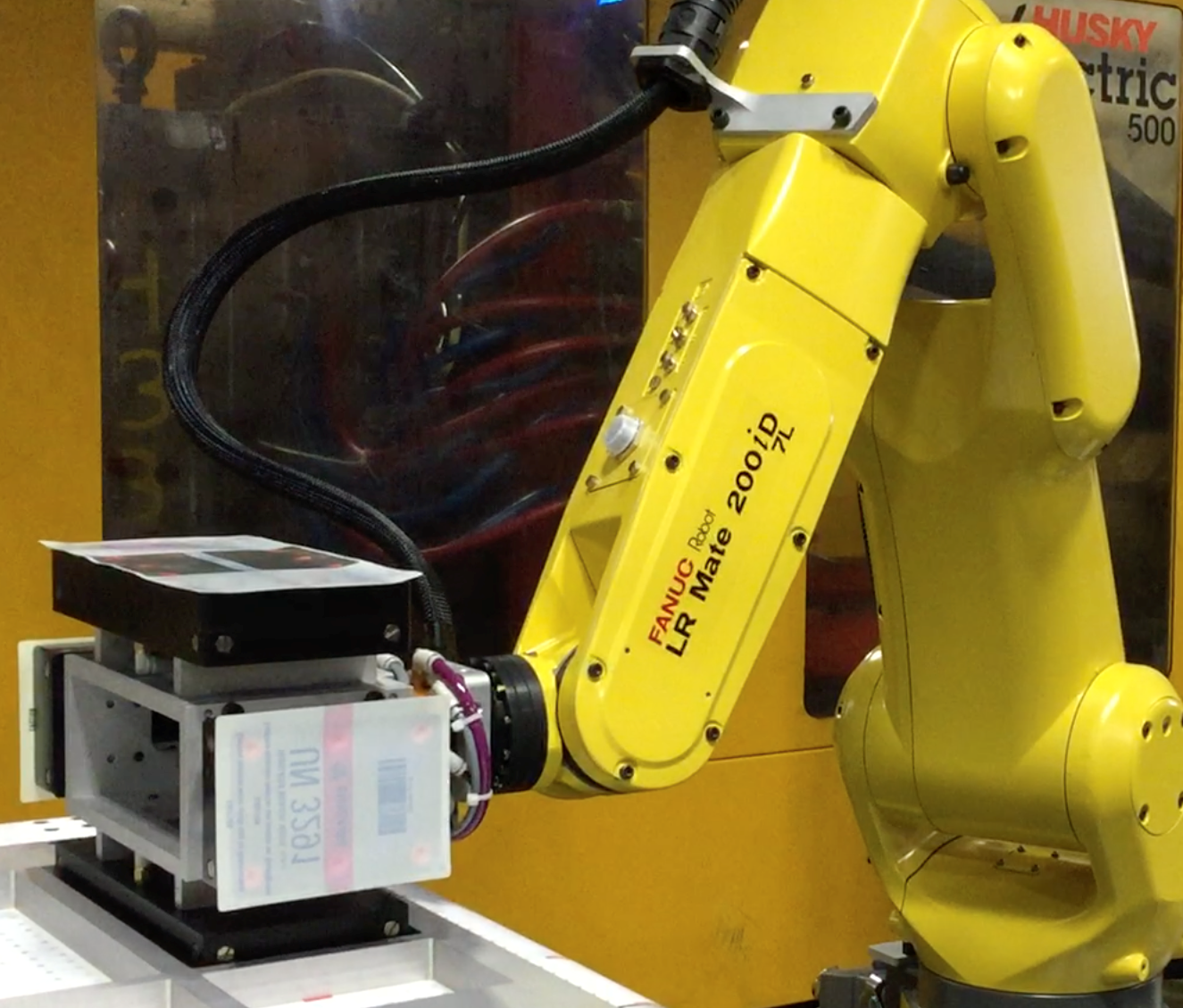
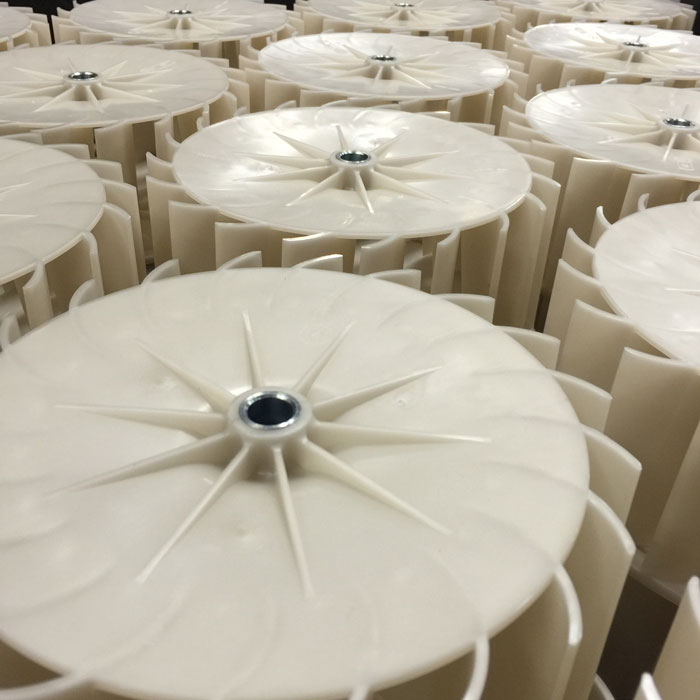
INSERT MOLDING
Insert molding is accomplished using the latest technology in robotics and automation. Applications include insert molding of various metal and plastic components, as well as electrical connectors, magnetic devices and numerous other unique inserts. From a single bearing automatically inserted to 27 inserts hand loaded to vision confirmation for insert accuracy, we have extensive experience in semi and fully automated insert molding. Commercial Plastics’ experienced engineering group can help you meet stringent requirements for bonding and locating insert and over-molded components in your next project.
Applications
• Bearing and threaded insert assembly
• Stainless steel and stamped metal assembly
• Rubber wear resistance assembly
• Electrical connection assembly
• Magnetic assembly
Advantages
• Critical assembly strength of metal vs. plastic
• Multiple physical property needs of a single material
• Faster assembly cycle times
• Elimination of secondary assembly material stresses
INTEGRATED VALUE-ADDED OPERATIONS
Our integrated value-added operations consist of, but not limited to in-line barcode part to part scanning and recording to living hinge activation and part assembly. We integrate many operations throughout our process that add value and efficiency. With over 70 robots we can design a fully integrated robotic cell or integrate a simple to complex secondary operation.
Advantages
• Living or Integral hinge parts
• Barcode scanning and recording
• Labor reduction
• Quality continuity
Integrated Assembly Cells
We specialize in automation assembly with millions of assemblies monthly. We have over 10 years of automated assembly and packaging experience from simple to intricate part assemblies to 100% automated palletizing. Our automation specialists can develop single cell to multi-cell automation systems in-house.
Advantages
• Reduce production and assembly cost
• Decrease in assembly cycle time
• Improved quality and reliability
• Reduce waste
Secondary Operations
In order to provide our customers with full service capabilities, CPC has a wide variety of conventional secondary operations. From operations as simple as printing a logo all the way to complex assembly, testing and fulfillment of an entire product line.
Bring your challenges to Commercial Plastics. We can offer you the most cost effective solution.
Some of our services:
• Multi-color Pad Printing
• Full part and package Assembly
• Kitting
• Heat Transfer
• Machining
• Sonic Welding
• Heat Staking
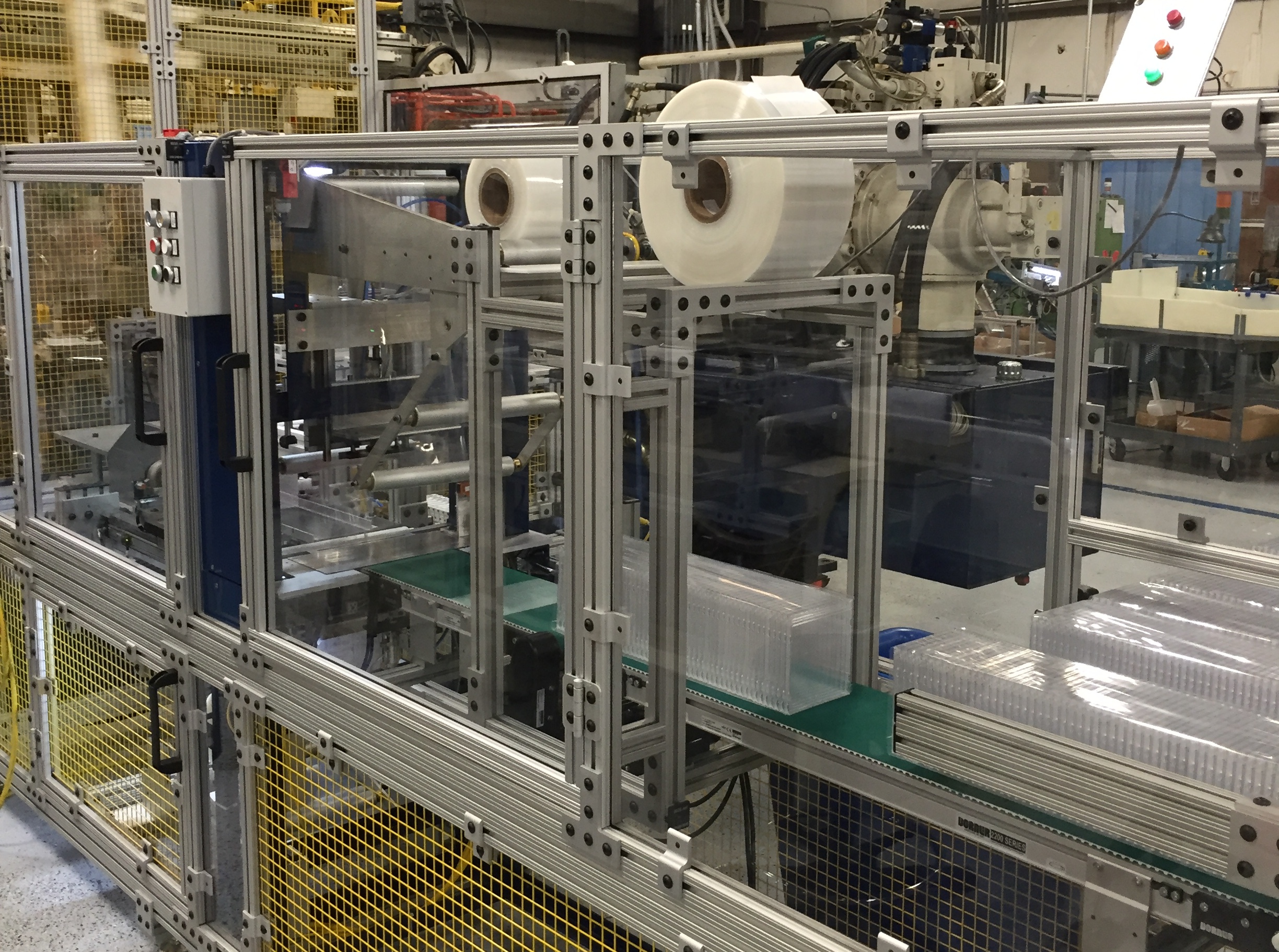
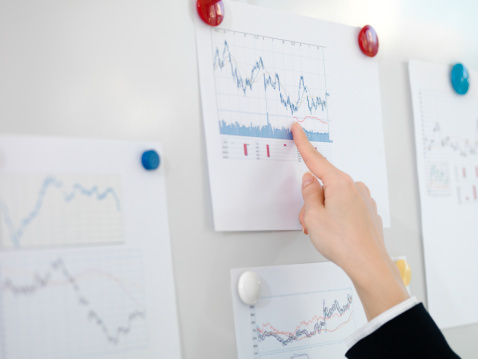
RJG eDart Process Monitoring
Our process validation starts with RJG. We utilize the RJG eDart system to validate the process and monitor the process to produce demanding parts. Process validation and complete process documentation are vital for our customers. This along with IQMS real-time monitoring gives CPC the quality assurance to keep that competitive edge.
Advantages
• Reduce scrap and processing time
• Record historical processing data on every shot
• Monitor critical information
• Real-time production monitoring
• Faster change-over of molds and inserts
• Increase quality assurance
• Understand which parameters are essential to product quality
Two-Shot Molding & Overmolding
Commercial Plastics has over 10 years experience in two-shot and over molding with cavity-to-cavity transfer or machine-to-machine automated cell transfer. We also have two barrel, two color or material stack mold capabilities. Our work cells are capable to large part cavity transfer two-shot molding to small magnet fully enclosed over-molding.
Applications
• Large part two-shot molding
• Thermoplastic polyurethane and elastomer over-molding
• Metal over molding
• Molded in gasket or liners
• Optically clear and infrared display
Advantages
• Soft feel and elastic performance
• Sound dampening and liquid proof sealing
• Multi-color and finish aesthetics
• Different material physical characteristics within a single part
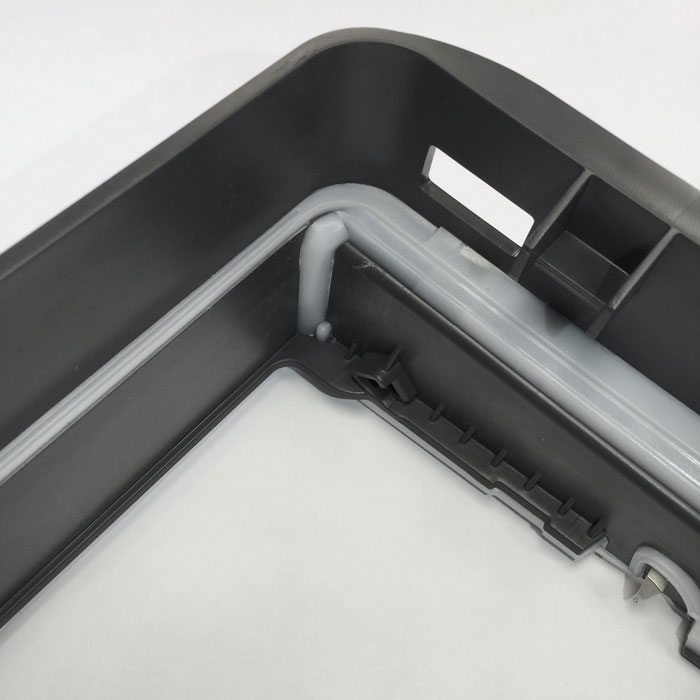